Applications of Illmenite Separators
The capacity varies considerably depending on metallurgical criteria. Most important variables are magnetic susceptibility characteristics of the magnetic particles, degree of liberation and size of the feed.
Mechanical features of the separator as tank design, magnet system and drum diameter do of course also effect the capacity. The following capacity figures can be used as guide-lines for STL magnetic wet separators in iron ore processing.
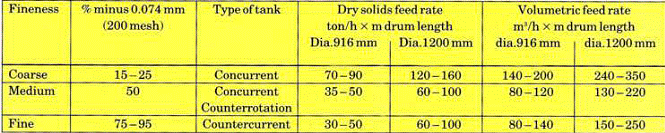
Above Figures applicable for iron ore processing.
As summary of the field experience and confirmed by test runs, following advantages can be emphasized when using the dia. 1200Mm separators specially for new projects:
- Reducing the total number of separators required.
- Lower operation and maintenance costs.
- Less number of pumps, pulp distributors, etc
- Less occupied floor space.
- Lower building cost.
SPECIAL APPLICATIONS
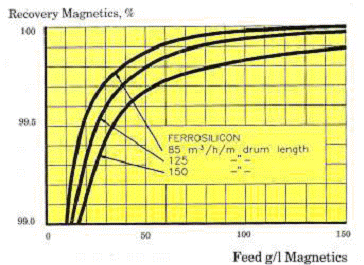
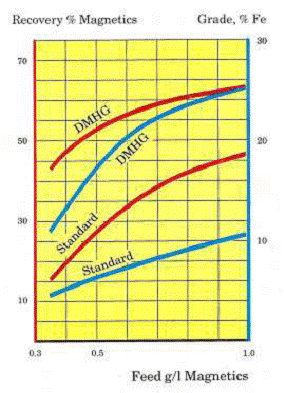
For applications involving fine or very fine particles, low content of magnetic material, and/or where highest recovery is desired, the HG- type magnetic assembly has been found to be superior to the standard assembly. The diagram to the right is an example on recovery of magnetite from floatation tailing s in true comparison with standard magnetic assembly.
The DMHG unit is designed to give a higher gradient than the standard assembly. The magnetic field strength is, however, lower. Thus the capacity measured as t/h x m drum length is down rated to correspond to the lower field rating.
The natural place for this separator is e.g. On a tailing s stream from a magnetite plant, secondary separator in a dense media recovery circuit, or recovery of metal powder production.
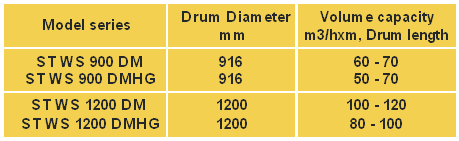
The above volume capacities are indicative for optimum performance at average conditions. Higher volumes can be allowed under special conditions.
chennai
design
exporters
globally
india
illmenite
manufacturers
sale
separators
suppliers
tamilnadu